WBPS explains how its E-Pod solution delivers flexible, cost-effective critical power, ensuring reliable and efficient operations for data centres.
For many years, WBPS has worked with several global data centre builders and operators and supported them in the design, supply, installation and commissioning of a range of critical power packages.
Today we are one of the leading suppliers of critical standby power to the UK data centre market. Using our significant experience and market insight, WBPS has designed and built a full plug and play critical power package for the data centre market.
A case study
We recently conducted a case study which looked at the way we deployed the full range of our WBPS E-Pod package, which was produced and installed for one specific global hyperscale data centre client.
Built off-site, the tested solution included a transformer, switchgear, generator, UPS, cooling, gantry, all interconnections between containers and full site commissioning which made this a full plug and play solution.
From the start, WBPS worked with the design team, offering full electrical and mechanical design support to ensure the client’s full range of requirements were catered for. The design process was undertaken with support from trusted partners and vendors preferred by the client. The equipment was packaged in the newly equipped facilities in Leicestershire, manned by specialist mechanical and electrical teams and over seen by a production manager.
The WBPS E-Pod solution offers plenty of flexibility in terms of equipment and the power ratings available. As well as providing a one-stop-shop, our data centre client was able to take advantage of maximum white space room for the external package, as well as more than 60% time savings compared with traditional builds. The E-Pod solution was also 50% cheaper to put into service over normal build and commissioning costs, helping to reduce delivery and installation timescales.
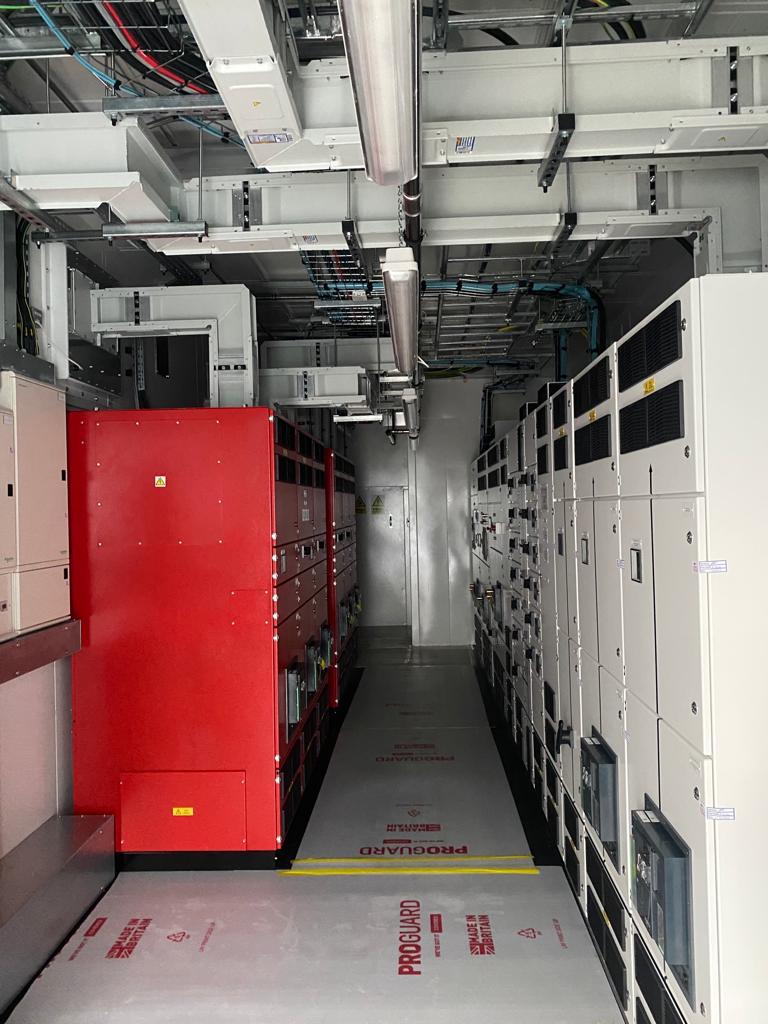
In this case study, the generator deployed was a Rehlko (formerly Kohler) model KD3500-E. Its engine was emission optimised and rated to deliver 3500kVA / 2800 kW DCP at 40°C. Other features included; a set mounted cooling system, dual circuit vertical radiator and an engine driven cooling fan.
The generating set control system selected by the client was the immensely capable Rehlko APM802. As well as being user-friendly and ergonomic, it also features autonomous operation of multiple generating sets and power plants. Its navigation via its 12 inch colour touch screen is 100% usable and intuitive without the need for an external computer.
The generating set was housed in a container rated to achieve a noise level of 65dBA at 1m FFC. The container has fully welded, bunded and sealed base area designed to accommodate the fluid capacity of the engine and radiator. Additionally, it had an outward opening door on each side and a water mist fire suppression system.
Fuel system
The generating set was fed from a 48 hour 35,000l bunded structural belly tank which sat below the generator container. The belly tank was filled via a fill point cabinet located at the front of the tank. Flexible fill lines ran internally from the tank to the generator base frame. A fuel safety system was installed which comprised of a free fall fire valve, tilt switch and fire wire.
Selective Catalytic Reduction (SCR)
The Rehlko engine offered low levels of NOx emissions, with these emissions further reduced by the addition of a roof mounted Selective Catalytic Reduction (SCR) system enabling the NOx levels to meet the most stringent of planning requirements. The AdBlue tank is located at the front of the container (adjacent to the fuel fill point) for ease of filling.
UPS pod
Each UPS Pod included a 2 x 1200kVA/1200kW UPS package complete with a 10-year design life stand mounted battery offering a full 10-minute end-of-life autonomy. The battery system also featured a battery circuit breaker and string isolation.
LV switchboard
There are two LV distribution boards housed in the package with internal power connections made using suitably rated busbar. The combined distribution boards have at their heart the mains/generator change over switchgear with outgoing feeds to the essential mechanical and data hall auxiliary services plus supplies to the dual UPS system and maintenance bypass.
Factory Acceptance Testing (FAT)
All the equipment was fully tested prior to leaving the manufacturer’s various factory locations. Each system was pre commissioned and FAT tested prior to dispatch from our packaging facility. The scope and duration of the testing was extensive and tailored to meet specific requirements of this client.
Commenting on the E-Pod solution, Andy Wilmott, CEO of the Wilmott Group and Managing Director of WBPS and Wiltech Acoustics Ltd says, “We have been able to draw on our insights in the data centre sector to create a backup power facility that is a real game changer. We know that no solution is perfect for every project, so using our design capabilities and project management expertise, we have developed a plug and play solution that can be adjusted according to individual requirements.
“Using Rehlko generating sets and a fuel system that has 48-hour capability, we have added a power pod that includes tripping batteries and USP that can manage internal essential services. Add to that health and safety requirements, a gantry system and commissioning, we will also maintain and service each installation as required. We are focused on building our data centre offer this year, and the launch of the Power-E cements our commitment to the sector.”
Commissioning
During the construction and installation phases of work, our Project Delivery Team, which includes the Commissioning Manager, worked closely with the client and nominated specialists to finalise the commissioning plan and programme. Once both the mechanical and electrical installations had been completed, the Commissioning Manager and his team set to work to commission and test all aspects of the installation. This culminated in a full Site Acceptance Test (SAT) including load testing fully coordinated with all other services providers working on the project.
Through life maintenance
With eight fully operational depots and over 90 field-based engineers based throughout the UK, WBPS are uniquely placed to offer a full and comprehensive preventative maintenance and four-hour emergency response to any client site.
The WBPS E-Pod packages contain a wide range of electrical equipment provided by our long-standing specialist partners who provide all necessary specialist maintenance and emergency support on their unique products. In this particular case study, WBPS were able to offer a seamless maintenance and support package on all equipment provided. For more information, visit: https://www.wbpsltd.co.uk/projects/wb-e-pod/